Back in the seventies, ISCAR introduced SELF-GRIP, the brand name of the original blockbuster parting tool design concept. According to the design concept of the SELF-GRIP tool (Fig. 1), a pressed carbide insert was clamped into a tool blade using the blade's elastic forces without the need for mechanical securing elements. At that time, other manufacturers also attempted to clamp inserts into a parting tool using the same principle. However, it was ISCAR that invented a reliable, truly workable concept that set the benchmark for parting applications.
The SELF-GRIP tool proved to be a game changer in parting. Shortly after its inauguration, similar designs by other producers appeared in the metal cutting market. ISCAR had already established its name as the authority in parting applications and quickly became the unrivaled leader in the industry. Today, there is no question why ISCAR's ongoing inventions of new parting tools attract great interest and deserve such close attention.
In parting, the rigidity of insert clamping is a key factor. The desire to achieve sensible and economical use of workpiece material dictates the ultimate reduction in cutting width. An increase in the diameter of the workpiece leads to the increase of the tool's overhang. The narrow width of the insert and the blade can degrade the tool's dynamic behavior and ultimately affects machining performance. Improving clamping rigidity and increasing the tool strength to assure effective cutting under unfavorable cutting conditions are key factors when designing a parting tool.
ISCAR's SELF-GRIP tool concept was a breakthrough, which aspires its prolific R&D engineers to continue improving the concept today. The "classical" SELF-GRIP tool line has been upgraded and considerably expanded with new geometries and remarkable approaches to parting metal productively. The evolution of ISCAR's parting tools exemplifies a logical progression of development by use of highly engineered solutions throughout several generations of R&D engineers.
Pinpointed high pressure coolant (HPC) provides competitive advantages for better parting performance by decreasing temperatures at the cutting zone and by assuring excellent chip breaking, which substantially improves surface finish and prolongs tool life. In machining difficult-to-cut heat-resistant superalloys and austenitic stainless steel, HPC reduces or even eliminates the built-up edge phenomenon. High pressure coolant is highly advantageous in parting operations.
The production of effective inner coolant channels in thin tool blades is a difficult engineering task. ISCAR has provided robust solutions to contend with this problem. One of these solutions is offered through DO-GRIP parting tools, developed several years after the successful launch of the SELF-GRIP tool line. A DO-GRIP tool carries an insert with two cutting edges situated at opposite ends. The edges are twisted relative to each other; thus, the non-working edge does not limit the cutting depth of the tool. (Fig. 2).
The PENTACUT family of tools that mount star-shaped carbide inserts were originally designed for parting small-in-diameter workpieces, tubes, and thin-wall parts. These cost-efficient inserts provide five indexable cutting edges and a highly economical utilization of tungsten carbide. The inserts are clamped in the insert pocket by a screw that passes through the insert’s central hole. The evolutionary stages of the 5 cornered insert proved to be difficult when utilizing PENTACUT inserts for large diameter workpieces. To successfully contend with this task, the insert needed to grow in size which made the task technically problematic and economically impractical.
The solution was found in the PENTA-IQ-GRIP – a family of parting tools that also mounts indexable inserts with five cutting edges. The family enables parting workpieces in diameters of up to 40 mm (1.5"). Due to an innovative dovetail securing principle, the tools utilize relatively small-sized inserts and provide highly rigid clamping which significantly increases tool life, improved part straightness and surface finish in parting applications. In addition, there are PENTA-IQ-GRIP tools with an HPC option (Fig. 3).
The SELF-GRIP clamping concept utilized the elastic behavior of a parting blade. This attribute paved the road for a new and improved parting system which took clamping stiffness to a new level. TANG-GRIP functions on the principle of supreme support for the insert to counteract cutting forces applied on the tool during the operation. (Fig. 4). The orientation of the slot that functions as an insert pocket was changed compared to the SELF-GRIP tool design, and therefore support is achieved by the long and rigid rear wall of the pocket. TANG-GRIP has a solid stopper, unlike the friction retaining force that characterizes most parting systems that feature a self-clamping insert. This mechanical design feature eliminates insert pull out during retraction. Significantly improved rigidity results in noticeably increased tool and pocket life. Together, with a robust insert design and a reinforced cutting edge, TANG-GRIP enables parting at exceptionally high feed rates, consequently increasing productivity to new extremes.
Notwithstanding, there appears to be another side of the 'parting' coin. Increasing the feed rate causes an increase of cutting force components. The situation worsens when the diameter of a bar and depth of penetration become larger. This results in blade deflection, which can become a significant factor in affecting the application. The method of utilizing Y-axis parting is a way to overcome the problem. The blade is loaded in a manner which is preferable. Y-axis parting is common on Multitasking machines with a Y-axis drive assuring appropriate feed motion, yet these machine types are not popular.
Compared to traditional parting along the X-axis, Y-axis parting substantially improves the blade's dynamic behavior by use of a tangential cutting force. When parting in the direction of radial forces, blade rigidity is reduced. Once again ISCAR's prolific R&D engineers invented a formidable winning solution by introducing LOGIQ-F-GRIP, a new tool family characterized by a square adapter with four inserts mounted on each of its cutting tips. (Fig. 5). The adapter combines both blade orientations (in X- and Y-directions) which provides a balanced-rigid design. The adapter has 4 insert pockets, and substantially prolongs tool life. If one of the pockets is damaged, the adapter can be indexed in a simple manner. The adapter is available with or without an internal HPC option and mounted in a robust block with reinforced ribs that assure a highly durable parting tool assembly. The impressive rigidity of the system results in highly stable efficient parting at narrow widths of cut, even when used for parting large-in-diameter bars while guaranteeing savings in raw material. The system is suitable for all types of lathes, regardless of whether they have a Y-axis drive.
When searching for the right parting tool, all manufacturers stand at the parting of the ways. ISCAR's milestones in creating revolutionary parting systems prove once again its commitment to advanced solutions to meet customer demands.
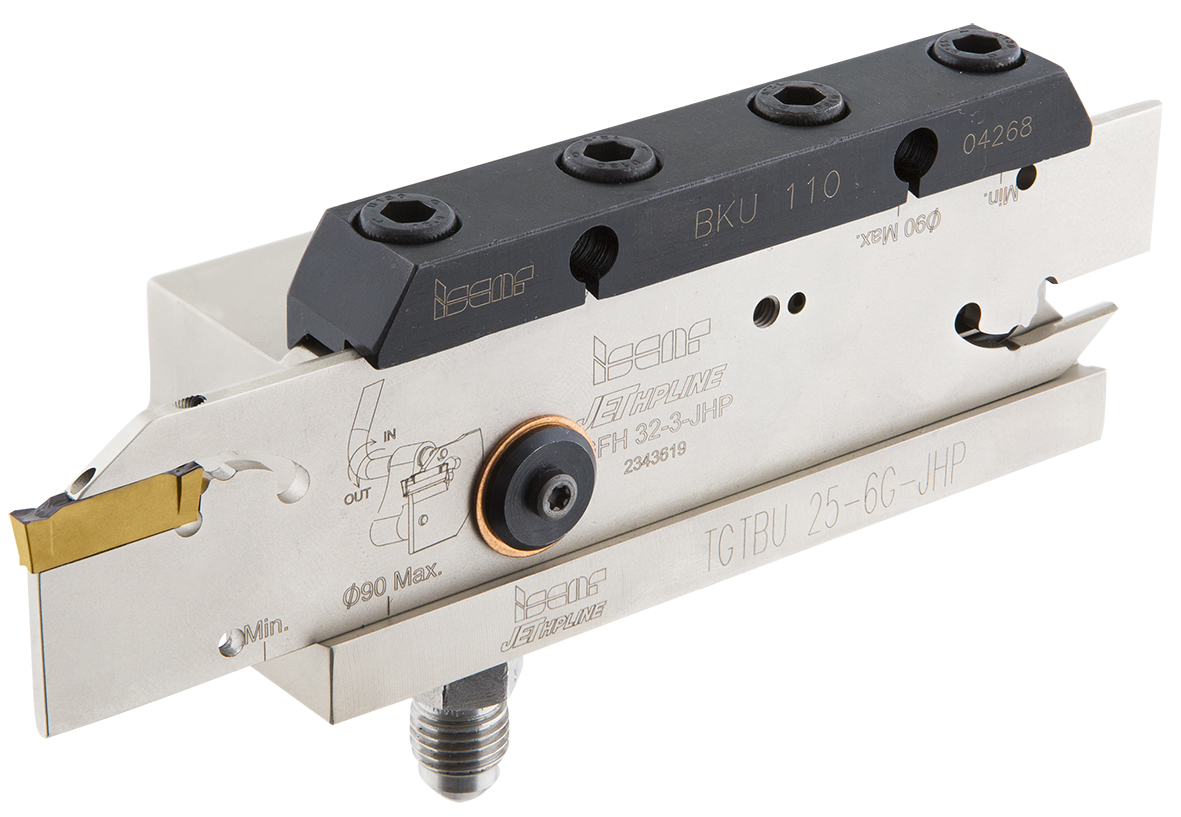
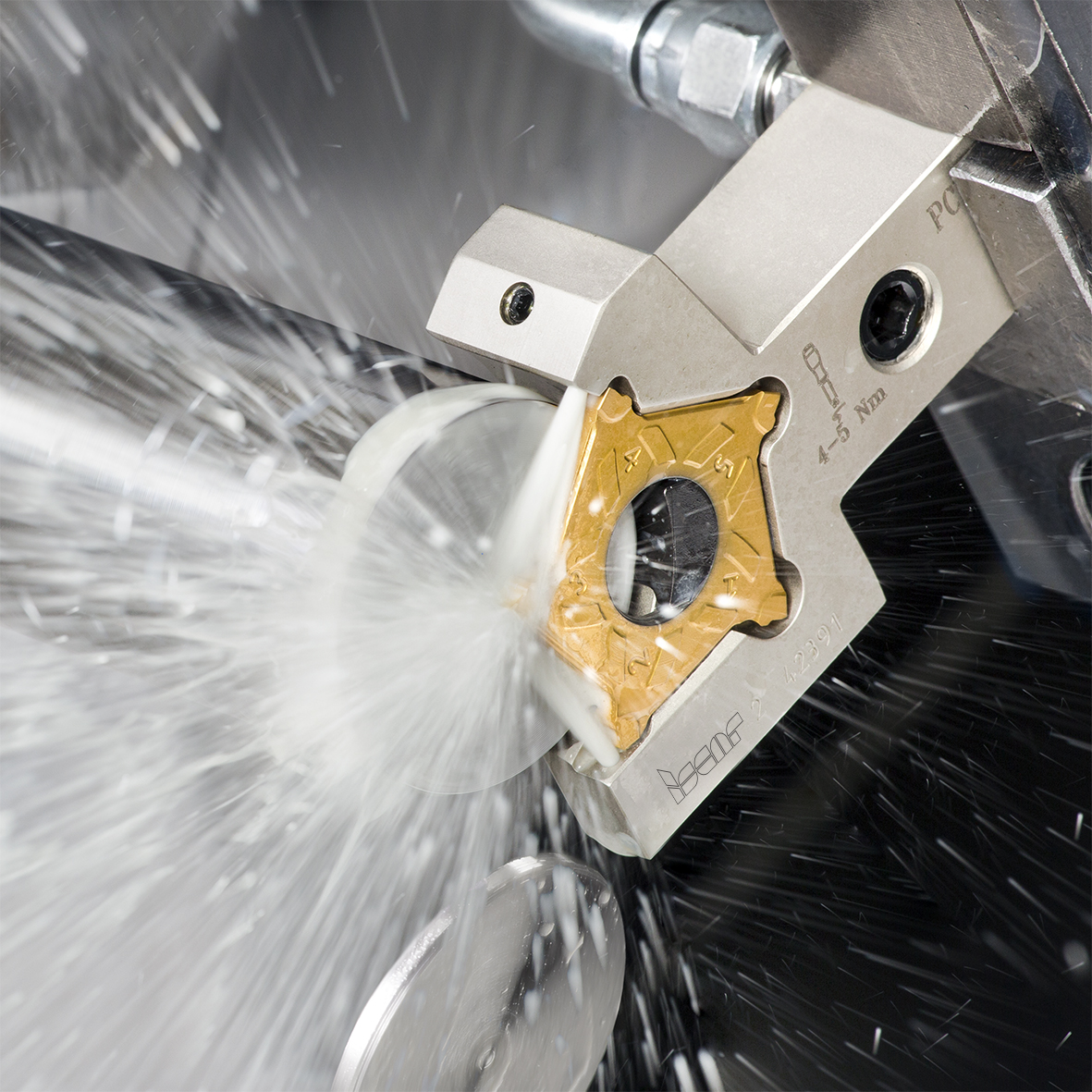
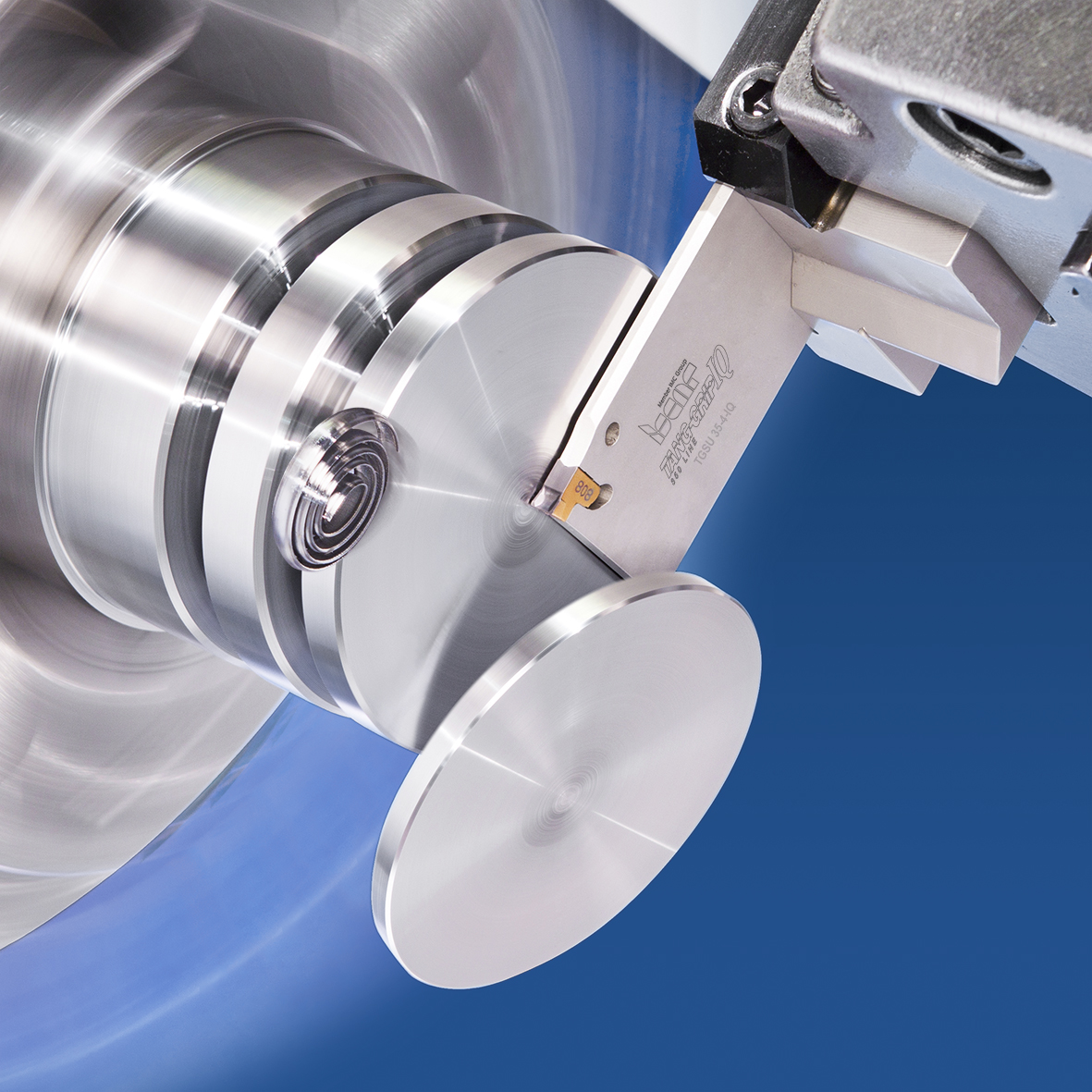
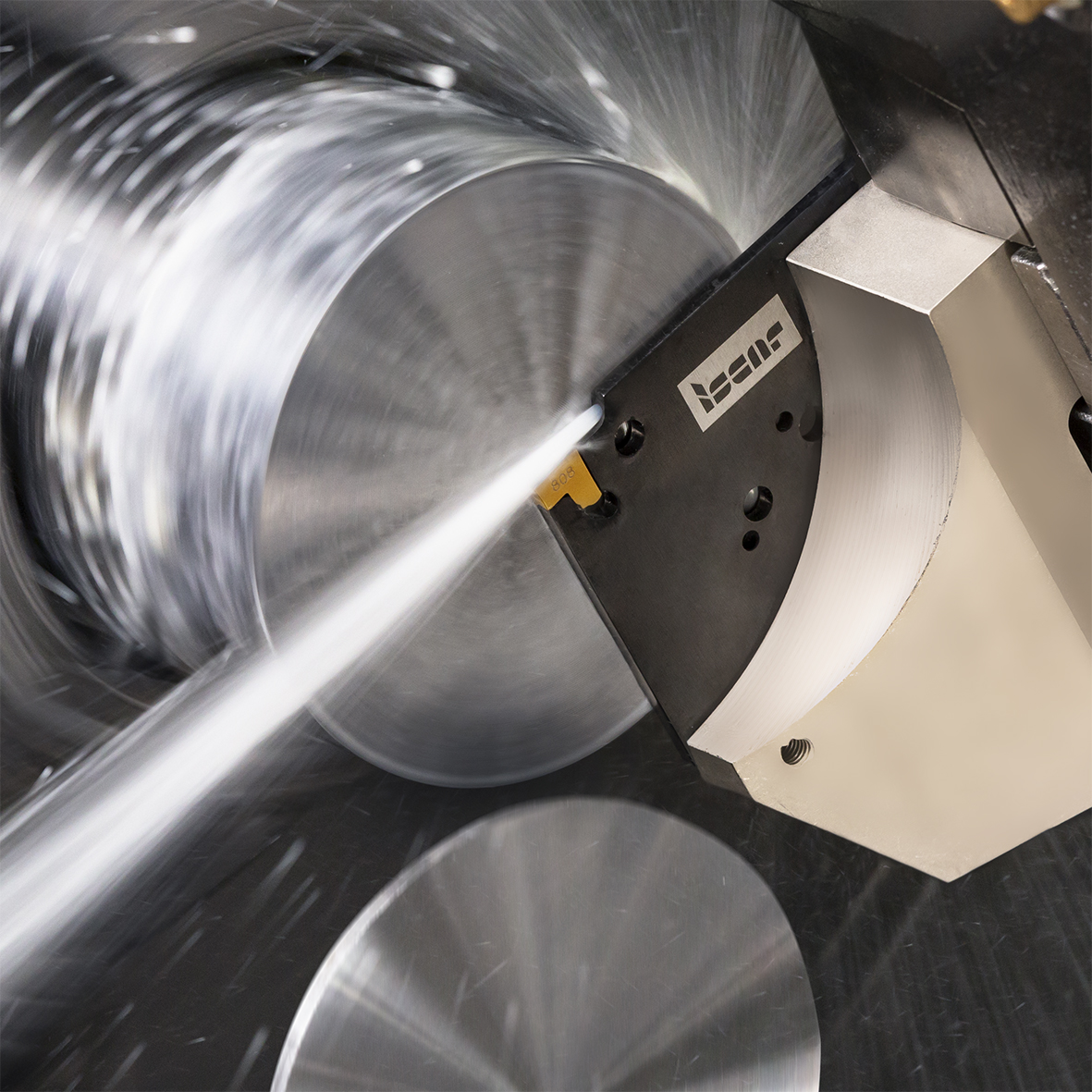